It is quite possible to reconcile, two things that seemed opposite not so long ago, thanks to the new technology. Reduce energy consumption and increase the performance of a machine. Pneumatic technologies for example are very inefficient, in some cases there is only 10% of the energy consumed that is used by the cylinders the rest is lost in heat and other losses in the system. In addition to generating more noise they require a compressor, an imposing amount of air preparation device (lubricator, regulator, accumulator, valve and silencer). The maintenance of these devices is intensive and in some cases the adjustment of the regulators is more witchcraft than technique. A change in temperature or humidity can result in a complete adjustment. Not to mention the replacement of the cylinders because the cousin at the end of the stroke no longer does its job or that the operator has changed the pressure of the system. LinMot has developed a linear motor that has the shape of a cylinder but the properties of a servo motor.
Stainless steel Servo Motor Guided LinMot
So complete control over speed and position. In addition, the technology does not include wear parts and requires very little maintenance. You will be able to increase the pace without breaking the equipment, in addition to an increase of efficiency ( 95% to 98%) , the solution is also not influenced by moisture. Once adjusted the actions will be repetitive and will not change over time. This results in a reduction in startup time and reduction of service calls on the machine.
Another technology that consumes quite a lot of energy is hydraulics. The efficiency of this technology is about 50% and also uses several more or less complex devices to make everything work 🙁 Pump, Regulator, Piping, Cooler, Valve and Oil Tank). Oil is increasingly becoming an environmental concern especially in food processes. There are vegetable oils but it is less durable and requires more maintenance. Oil changes generate waste that can be potentially mismanaged
There are linear positioning technologies in the form of cylinder, belt or rack and pinion that are powered by a Servo motor that have an efficiency of more than 90%.
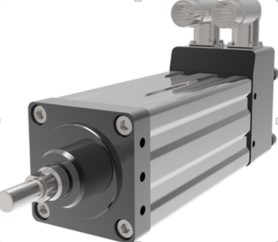
Their accuracy is better and so is their durability. For the most part maintenance-free other than lubrication of their bearings they present less risk to the environment and are much greener and more efficient technologies.
Another source to improve your energy efficiency is to favour high-efficiency speed reducers. Worm Gear type gearboxes generally have a low efficiency VS Planetary or helical gearbox. So pay attention to the choices of your gearboxes and try to choose products in the 90% efficiency. There is up to 40% energy saving possible. Especially in large gear ratio .
There also other benefit with lower friction comes lower heat dispassion , so your gearbox run cooler and you will need less BTU to cool down your plant. Your Oil and Seals will also last longer.
Here are some reference articles for you
Comparing-the-Cost-of-Pneumatic-to-Electric
Choosing-Electric-over-Hydraulic-Actuation
In summary it is possible to improve productivity and reduce operating costs if you go electric . New technologies are more expensive but if we take into account the total cost of ownership they become more competitive than traditional linear fluid power option.
In addition the servo drive technologies are already ready for Industry 4.0, You will have a more efficient process in addition of having more data on the process.
For example your drive know in all time : Position and Speed
We are available to work with you on your energy saving program or your machine conversion program
Feel free to contact us